Manufactured By: Thermo Fisher Scientific
Simulating production conditions in the pilot plant
Dies are used in addition to extruders for testing the rheological characteristics and processability of polymers and for producing laboratory test samples.
Dies enable the defined geometries for profiles, films or rheological measurements. Both dies and PostEX units closely resemble their larger-scale “big brothers” to ensure production-like testing is guaranteed. Integrated measuring sensors further enhance the application possibilities in the laboratory or pilot plant.
Measuring dies in laboratory applications
Measuring dies create profiles of a defined geometry to make special test specimens that may be inspected with other techniques or to simulate a production process such as film blowing, wire coating or catheter extrusion. Temperature and pressure probes in the die monitor the behaviour of the sample online. The flow geometries accommodate the behaviour of different polymer types during extrusion.
The Thermo Scientific HAAKE PolyLab OS System and Thermo Scientific HAAKE PolyLab QC System can be transformed into a powerful extrusion capillary rheometer when used together with rheological dies. Rheological data such as shear stress and viscosity functions can be evaluated. These are of great importance for the design of injection moulds, extruders and extruder screw design. The shear rate ranges experienced during polymer processing can be fully covered using both rod and slit capillary dies.
Blown Film Die
Blown Film Die
Film production simulation for polymer development, materials evaluation and parameter monitoring requires highly adaptive, small scale systems with complete process functionality. The PolyLab System and RheoMex extrusion line, in conjunction with a blown film die and take-off tower system, provide a means of accurate thin film production for total process evaluation with less than 1kg of material.The blown film die is used in conjunction with a laboratory extruder. The molten polymer is formed into a thin walled tube by being forced through a ring gap located at the end of the die. The inside of the extruded tube is inflated by air pressure.
Catheter/Tubing Die
Catheter Die
The catheter die is designed for tubes with diameters of about 2 to 8 mm. This die is ideal for producing capillary and catheter tubes. The process is supported by an air supply in the inner tube to prevent a collapsing of the small tubes.
Filter Die
Filter Die
The filter die is suitable for testing colorants in the form of colour concentrates (master batches) in all polymers used for extrusion and melt-spinning processes. The design follows the EN standard 13900-5. The pressure increase before of a standardised melt filter is measured, from which the FPV (Filter Pressure Value) is calculated thus indicating the dispersion quality of the master batch.
Garvey Die
Garvey Die
The Garvey die adheres to ASTM 2320 and can be used to examine the flow behaviour of material, especially rubber, to continuously fill the different angles of the die. Its shape simulates the typical design of tire building blocks such as the thread and apex or parts of the side wall.
Horizontal/Vertical Rod Die
Horizontal Die
The rod die produces a single strand for inspections or pelletising. The inter-changeable nozzles on the horizontal rod die vary not only in diameter but also in length to supply different pressure ranges and die swell information.
Multi Strand(3 Strands) Die
Multi Strand Die
In a pelletising application it is sometimes of great advantage to have a high output rate while maintaining a sort strand and slower output speed. This is the dedicated application of the multi strand die. When combined with the HAAKE water bath and pelletiser, the complete lab-scaled pelletise line can be set up.
Rod Capillary Die
Rod capillary Die
This die is designed to measure the absolute viscosity of polymers. It provides a tool with interchangeable capillaries. The pressure is measured directly before the capillary entrance. The nozzles are wear reduced for long life reproducibility and the testing of filled polymers and ceramics. Depending on testing material and nozzles, shear rates between 50 – 200,000 1/s can be achieved.
Sheet Die
Sheet Die
These dies produce sheets of different width and thickness. The optimized flow channel produces a ribbon of homogeneous output. The flexible die lip option enables the on-site adjustment of the sheet thickness as well as an optimization of the diameter.
Slit Capillary Die
Slit Capillary Die
This die enables a measurement of pressure gradient and melt temperature directly within the slit capillary. Thus the absolute viscosity of a polymer can be determined. Different geometries are available to adapt the die to the shear rate and the viscosity range. Depending on the geometry and testing material shear rates of 10 – 1,000 1/s are possible.
Spinning Die
Spinning Die
The spinning die enables the simulation of a fibre spinning process in a lab scale. The standard die extrudes 10 fibres with an initial diameter of 0.2 mm. By exchanging the spinning plate, other geometries are possible.
Wire coating Die
Wire coating Take Off Die
The wire coating die forms a constant coat on wires in different diameters. The die utilises an adjustable mandrel to provide a fine tuning of the concentricity of the coating. In combination with the wire coating take-off it forms a complete lab scaled processing unit.
Elongational / X- Die
Elongational or X-Die
The HAAKE X-die is the first easy to use and reliable technique that can provide either an on-line and continuous measurement of the apparent elongational viscosity or the apparent elongational rate dependence of the apparent elongational viscosity.
Additional Product Information:
Item |
Size |
Download |
Product Brochure |
1.01mb |
Download |
Product Specifications |
199kb |
Download |
To download and view these attachments you must have Acrobat Reader. If you do not have Acrobat Reader, click the “Get Adobe Reader” button.
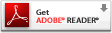